Integrated Safety Management
Integrated Safety Management is a framework developed by the U.S. Department of Energy for achieving its mission while maintaining the highest standard of safe operations. As adapted by UCLA, Integrated Safety Management is an iterative process consisting of five steps which are outlined in Figure 1 below. UCLA’s Risk Assessment Process will assist PI’s and their research groups in formalizing three of the five steps: assessing the risks, developing and implementing controls, and providing feedback.
Risk Assessment Process
EH&S will help your lab implement Integrated Safety Management through a 3-year cycle. This begins with an initial walkthrough of your laboratory designed to help you identify hazards and assess your existing mitigation strategies. EH&S will then meet with you and your research group and assist in the development of a Safety Management Plan specific to your laboratory and your research. A series of follow-up visits will be used to verify that your plan is effective, and provide opportunities for appropriate course-corrections as your research changes.
Step 1: Assessing Risk in the Laboratory
EH&S will work with your research group to conduct a hazard assessment of your laboratory. This hazard assessment will identify the risks associated with your work. Once the risks have been identified, they can be assessed and prioritized for mitigation.
Many risk assessment models use “severity of consequences” and “probability of occurrence” scales to rate risks associated with laboratory experiments (Table 1 and Table 2). They are a tool used for a more comprehensive assessment that not only prioritizes certain laboratory operations for mitigation, but also assists in the evaluation of proposed mitigation strategies.
An important element of risk assessment is the consideration of impacts beyond those to the individual researcher or laboratory. Not only can major incidents result in death or serious injury, but they may require that institutional-level resources be marshalled in order for operations to resume, and may damage the university’s reputation for years.
In addition to assessing the potential consequences of a given risk, the likelihood of those consequences occurring should also be assessed. The cumulative impact of minor injuries that occur on a regular basis may warrant prioritization over risks that may have greater consequences, but are very unlikely to occur.
Using this kind of scaling, laboratory hazard risk rating is determined as follows (Figure 2):
Risk Rating = Probability of Occurrence x Severity of Consequences
Severity of consequences is scored in this model using a weighted scale. This ensures that any operation which could result in death or major disruptions are more highly prioritized and that significant steps will be taken to mitigate that risk.
Step 2: Developing and Implementing Controls
Based on the assigned risk level, EH&S expects that PIs will take an appropriate response as described in Table 3.
Strategies for mitigating risk can be assessed using the Hierarchy of Controls framework (Figure 3). This approach is promoted by many safety organizations, including the National Institutes for Occupational Safety and Health. It organizes mitigation strategies, or controls, in order of effectiveness – from elimination of the hazard at the top, to personal protective equipment at the bottom. Under this framework, one should first consider the feasibility of the more-effective controls (e.g. substitution) before considering less-effective measures (administrative controls).
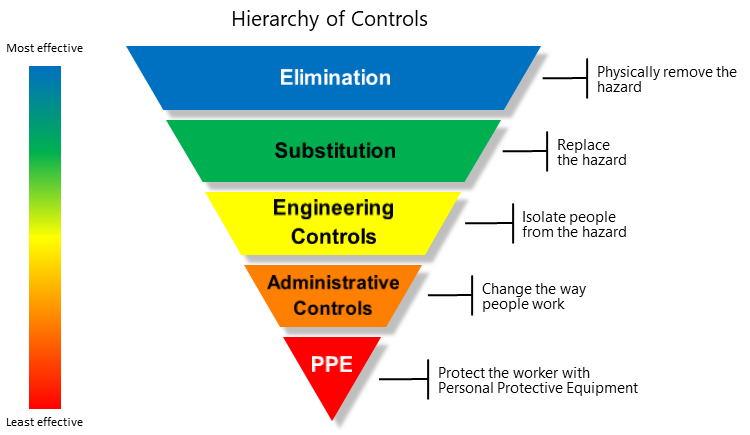
Step 3: Providing Feedback
A successful Safety Management Plan will detail mechanisms for providing internal feedback and making adjustments. As research directions change, new hazards may be introduced to the laboratory. Personnel turnover is also an inherent fact of academic research, requiring that laboratory responsibilities be reassigned on a routine basis. Additionally, unanticipated risks may present themselves through observation of one’s experiments, especially in the form of lessons learned through incidents and near-misses.
Step 4: View Sample Safety Management Plan
You can view an example plan here.
Step 5: Read the Risk Assessment FAQ
Read the FAQ.